Spis treści
Co to jest Lean?
Lean to podejście do zarządzania, które stawia na minimalizację marnotrawstwa i maksymalne podnoszenie wartości z perspektywy klienta. Kluczowym elementem tej filozofii jest identyfikacja i eliminacja wszelkich strat w procesach, a także ich ciągłe doskonalenie. Istotą Lean jest aktywne zaangażowanie pracowników w wykrywanie problemów i wdrażanie usprawnień, co z kolei przekłada się na efektywniejsze funkcjonowanie całej organizacji. Co więcej, włączenie pracowników w proces ulepszania nie tylko podnosi ich motywację, ale również daje każdemu poczucie realnego wpływu na rozwój firmy.
Co to są fundamenty Lean w produkcji samochodów?
Filozofia Lean w produkcji samochodów bazuje na kilku filarach, których celem jest usprawnienie procesów i dostarczenie klientowi maksymalnej wartości. Kluczowe elementy to:
- redukcja zapasów do minimum, co pozwala na osiągnięcie płynnego przepływu produkcji,
- wytwarzanie zgodnie z zasadą „just-in-time„, co oznacza, że komponenty i materiały są dostępne dokładnie wtedy, gdy są potrzebne,
- standaryzacja pracy,
- ciągłe doskonalenie, znane jako Kaizen, stanowiące fundament dalszego rozwoju.
Wdrożenie tych zasad przekłada się na konkretne korzyści:
- znaczące zwiększenie efektywności operacyjnej,
- redukcja kosztów produkcji,
- poprawa jakości wyrobów.
W rezultacie firma może efektywnie odpowiadać na potrzeby klientów, zapewniając im satysfakcję. Dobrym przykładem zastosowania tych zasad w praktyce jest system produkcyjny Toyoty, który stanowi doskonałą ilustrację skuteczności podejścia Lean.
Jakie są podstawowe narzędzia Lean do codziennej pracy?
Narzędzia Lean to nieocenione wsparcie w codziennej pracy, umożliwiające identyfikację i eliminację źródeł strat oraz usprawnienie procesów. Do kluczowych zaliczamy:
- Mapowanie Strumienia Wartości (VSM),
- 5S,
- SMED,
- TPM,
- Pracę Standaryzowaną,
- PDCA,
- Rozwiązywanie Problemów metodą A3.
Mapowanie Strumienia Wartości (VSM) to wizualizacja przepływu materiałów i informacji niezbędnych do wytworzenia produktu lub usługi, która pomaga zidentyfikować obszary wymagające poprawy, takie jak opóźnienia czy wąskie gardła. Metodyka 5S, obejmująca Selekcję, Systematykę, Sprzątanie, Standaryzację i Samodyscyplinę, koncentruje się na utrzymaniu porządku i organizacji w miejscu pracy, co przekłada się na wyższą efektywność i bezpieczeństwo, gwarantując na przykład, że każde narzędzie ma swoje wyznaczone miejsce. SMED (Single Minute Exchange of Die) to technika redukcji czasu przezbrojeń maszyn, zwiększająca elastyczność produkcji, ponieważ krótsze przezbrojenia pozwalają na efektywniejsze wykorzystanie czasu produkcyjnego. TPM (Total Productive Maintenance) to system angażujący wszystkich pracowników w dbałość o maszyny i urządzenia, minimalizując ryzyko awarii i przestojów dzięki regularnym przeglądom. Praca Standaryzowana definiuje optymalny sposób realizacji zadania, zapewniając spójność i efektywność wykonywanej pracy, dzięki czemu każdy pracownik posiada jasne wytyczne dotyczące swoich obowiązków. PDCA (Plan-Do-Check-Act) to cykliczny proces ciągłego doskonalenia, polegający na planowaniu, wdrażaniu, weryfikacji i wprowadzaniu ulepszeń. Rozwiązywanie Problemów metodą A3 to systematyczne podejście do analizy i rozwiązywania problemów, w którym wszystkie informacje są prezentowane na jednej kartce A3, co usprawnia komunikację i współpracę zespołową.
Jakie techniki oferuje Lean Management?
Lean Management to zestaw sprawdzonych strategii, które usprawniają firmowe procesy i redukują marnotrawstwo. Wśród kluczowych narzędzi znajdują się:
- mapowanie Strumienia Wartości (VSM),
- metoda 5S,
- system Kanban – wizualizujący przebieg zadań,
- poka-yoke, czyli zabezpieczenia chroniące przed pomyłkami,
- jidoka, umożliwiająca automatyczne wstrzymanie linii produkcyjnej w razie wykrycia jakiejkolwiek nieprawidłowości,
- heijunka koncentrująca się na równomiernym rozłożeniu obciążenia produkcyjnego,
- kaizen, czyli filozofia nieustannego doskonalenia,
- system ssący (pull system).
Integracja tych metod przynosi wymierne korzyści dla przedsiębiorstwa. Przykładowo, podnosi standardy jakości oferowanych produktów i usług, usprawnia zarządzanie zapasami w magazynie, a proces produkcyjny zyskuje na elastyczności. W rezultacie, organizacja funkcjonuje efektywniej i sprawniej reaguje na oczekiwania konsumentów. Główny cel to eliminacja wszelkich działań i elementów, które nie wnoszą wartości dla klienta, a jednocześnie absorbują firmowe zasoby.
Jak zidentyfikować i wyeliminować marnotrawstwa w Lean?
Identyfikacja i eliminacja marnotrawstwa stanowi fundament szczupłego zarządzania. Aby skutecznie to osiągnąć, należy w pierwszej kolejności rozpoznać siedem głównych typów marnotrawstwa, znanych pod japońskim terminem Muda. Wśród nich wyróżniamy:
- nadeksprodukcję,
- czas oczekiwania,
- zbędny transport,
- nadmierne przetwarzanie,
- nadmierne zapasy,
- niepotrzebne ruchy,
- defekty.
Mapowanie Strumienia Wartości (VSM) okazuje się nieocenionym narzędziem w metodyce Lean, pozwalającym na precyzyjne wskazanie obszarów generujących straty w procesach, ujawniając na przykład ukryte przestoje w produkcji. Dodatkowo, metoda 5S, nastawiona na utrzymanie porządku i wzorowej organizacji, stwarza solidną podstawę dla zwiększenia efektywności. Warto również wspomnieć o systemach ssących (pull), które ograniczają ryzyko wystąpienia nadmiaru zapasów, opierając się na realnym zapotrzebowaniu, a nie na prognozach. Filozofia Kaizen, czyli ciągłe doskonalenie, zachęca do nieustannego poszukiwania usprawnień w każdym aspekcie działalności. Aby skutecznie identyfikować marnotrawstwo, niezbędne jest aktywne uczestnictwo całego zespołu. Każdy pracownik powinien angażować się w analizę procesów, koncentrując się na wyeliminowaniu działań, które nie przynoszą wartości dodanej dla klienta. Po zidentyfikowaniu obszarów problemowych, kluczowe staje się wdrożenie konkretnych działań naprawczych, na przykład poprzez optymalizację układu linii produkcyjnej czy udoskonalenie harmonogramu konserwacji.
Jakie są korzyści z wdrażania Lean w miejscu pracy?
Wdrożenie Lean w firmie to inwestycja, która przynosi wymierne korzyści w wielu kluczowych obszarach działalności. Przede wszystkim, przekłada się to na znaczny wzrost efektywności dzięki lepszemu wykorzystaniu dostępnych zasobów, co bezpośrednio wpływa na sukces przedsiębiorstwa. Co więcej, Lean to także redukcja kosztów. Eliminując marnotrawstwo, takie jak nadmierna produkcja czy niepotrzebny transport, firma minimalizuje straty finansowe i optymalizuje wydatki. Poprawa jakości produktów i usług to kolejny istotny efekt. Dzieje się to za sprawą eliminacji defektów i wprowadzenia standaryzacji procesów. Skrócenie czasu realizacji zamówień również jest nie do przecenienia. Optymalizacja procesów wraz z eliminacją przestojów ma decydujące znaczenie dla sprawnego działania. Naturalną konsekwencją terminowości i wysokiej jakości jest rosnąca satysfakcja klientów, co przekłada się na ich lojalność. Warto podkreślić, że Lean to nie tylko aspekty finansowe i operacyjne. To także wzrost zaangażowania pracowników, których włącza się w proces doskonalenia i obdarza odpowiedzialnością, co znacząco podnosi ich motywację. W perspektywie długoterminowej, Lean kształtuje kulturę ciągłego doskonalenia, umożliwiając firmie elastyczne reagowanie na zmiany rynkowe i budowanie trwałej przewagi konkurencyjnej.
Jak zbudować zespół do wdrażania Lean?
Stworzenie efektywnego zespołu Lean wymaga zaangażowania osób reprezentujących różne działy i szczeble w firmie. Kluczowe jest, aby jego członkowie charakteryzowali się otwartością na konieczne transformacje. Niezwykle istotna jest również umiejętność logicznego myślenia, wsparta pragnieniem ustawicznego rozwoju. Idealny skład takiego zespołu cechuje różnorodność – obok liderów warto uwzględnić także pracowników liniowych. Takie połączenie perspektyw zapewnia holistyczne spojrzenie na procesy i umożliwia identyfikację problemów z wielu punktów widzenia. Liderzy, oprócz motywowania pozostałych członków, aktywnie eliminują przeszkody, podczas gdy pracownicy liniowi wnoszą bezcenną wiedzę na temat codziennych trudności.
Aby skutecznie pełnić swoją rolę, liderzy zespołu Lean powinni nieustannie doskonalić swoje kompetencje. Pomocne w tym są regularne ćwiczenia kata, wspomagające rozwiązywanie problemów i wdrażanie usprawnień. Ponadto, szkolenia z zakresu narzędzi Lean stanowią niezbędny element wyposażenia każdego członka zespołu, umożliwiając identyfikację obszarów wymagających poprawy i implementację innowacyjnych rozwiązań. Oprócz umiejętności analitycznego myślenia i generowania kreatywnych rozwiązań, członkowie zespołu Lean powinni wykazywać się samodzielnością oraz umiejętnością pracy w grupie. Kluczowe jest nieustanne zaangażowanie w proces doskonalenia – tylko wtedy można osiągnąć trwałe i realne zmiany.
Zespół Lean koncentruje się na:
- identyfikacji obszarów wymagających optymalizacji,
- opracowywaniu i wdrażaniu konkretnych rozwiązań,
- monitorowaniu efektów wprowadzonych zmian.
Niezwykle ważna jest kultura Lean, która promuje zaangażowanie pracowników, stwarza sprzyjające środowisko dla innowacji, a także wspiera dzielenie się wiedzą i otwartą komunikację o problemach. Aktywne poszukiwanie rozwiązań stanowi fundament skutecznego zespołu Lean.
Jak wdrożyć Lean w organizacji?
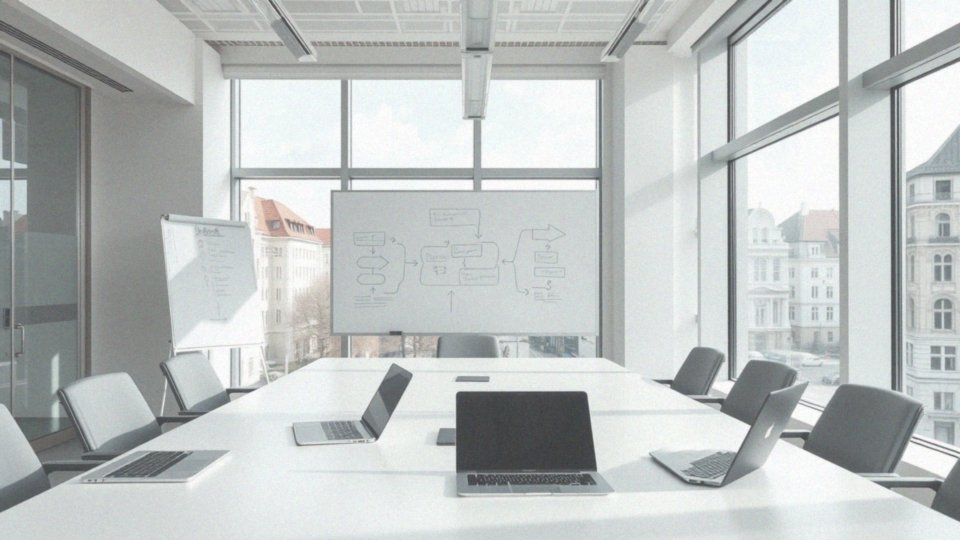
Wdrożenie Lean to prawdziwa transformacja dla firmy, dlatego wymaga przemyślanego planu i konsekwentnej realizacji. Na samym początku warto dokładnie przyjrzeć się obecnej sytuacji przedsiębiorstwa i zidentyfikować obszary, które najbardziej potrzebują usprawnień – gdzie konkretnie pojawiają się straty? Następnie, na podstawie tej diagnozy, opracuj szczegółowy plan wdrożenia, precyzując konkretne cele, tworząc realistyczny harmonogram i przydzielając odpowiednie zasoby. Kluczowym elementem sukcesu jest aktywne zaangażowanie wszystkich pracowników. Zadbaj o odpowiednie szkolenia, dzięki którym zrozumieją oni zasady Lean i będą mogli aktywnie uczestniczyć w procesie doskonalenia. Równie ważne jest bieżące monitorowanie postępów i analizowanie wyników, co pozwoli na szybką reakcję i dostosowanie strategii w razie potrzeby. Celem jest, aby ciągłe doskonalenie stało się integralną częścią kultury organizacyjnej, trwałym elementem codziennego funkcjonowania firmy. W ten sposób Lean może rzeczywiście zrewolucjonizować organizację, wpływając na codzienne nawyki i usprawniając nie tylko procesy produkcyjne, ale również komunikację w zespole. Krótko mówiąc, Lean to prawdziwa rewolucja w sposobie działania firmy.
Jak wygląda transformacja Lean w organizacji?
Transformacja Lean to prawdziwa rewolucja w przedsiębiorstwie, opierająca się na idei nieustannego doskonalenia, w którą angażują się wszyscy pracownicy, dążąc do optymalizacji procesów. Nie chodzi tu tylko o wdrożenie narzędzi Lean, ale przede wszystkim o zmianę sposobu myślenia każdego z nas. Celem tej przemiany jest znaczący wzrost efektywności, innowacyjności oraz jakości oferowanych produktów i usług, które mają stać się jeszcze lepsze. Kluczowe jest, aby każdy pracownik rozumiał fundamenty filozofii Lean, w tym koncepcję Kaizen, i aktywnie w niej uczestniczył. Dlatego też, stwórzmy wspólnie kulturę ciągłego doskonalenia, która obejmie każdy szczebel naszej organizacji.
Jak Lean wpływa na efektywność produkcji?
Lean, podejście skoncentrowane na usprawnianiu procesów i redukcji strat, ma zasadniczy wpływ na wydajność produkcji. Dąży się w nim do pełnego wykorzystania dostępnych środków, skrócenia czasu potrzebnego na realizację zadań oraz obniżenia kosztów. Dzięki temu przedsiębiorstwa, które wdrażają zasady Lean, mogą liczyć na wzrost produktywności i umocnienie swojej pozycji na rynku.
Efektywność produkcji w myśl filozofii Lean przejawia się w różnorodny sposób:
- skrócenie czasu cyklu produkcyjnego dzięki optymalizacji poszczególnych etapów wytwarzania,
- redukcja kosztów poprzez eliminację marnotrawstwa i racjonalne gospodarowanie zasobami,
- poprawa jakości wyrobów, będąca wynikiem skupienia na eliminacji wad i stałym doskonaleniu,
- zwiększona elastyczność, umożliwiająca firmom szybsze reagowanie na zmieniające się wymagania klientów i dynamikę rynkową,
- optymalizacja wykorzystania zasobów, zarówno ludzkich, jak i materiałowych,
- poprawa przepływu materiałów i informacji, co zapobiega przestojom i opóźnieniom.
Krótko mówiąc, Lean stanowi fundament sukcesu w nowoczesnym przemyśle.
Dlaczego kultura Lean jest ważna dla zaangażowania pracowników?
Kultura Lean, której fundamentem jest nieustanne dążenie do perfekcji, odgrywa zasadniczą rolę w budowaniu zaangażowania zespołu. Umożliwiając pracownikom aktywny udział w procesie decyzyjnym, Lean sprawia, że czują się oni współodpowiedzialni za losy firmy i mają realny wpływ na jej funkcjonowanie. Docenianie ich innowacyjnych idei i proaktywnych inicjatyw sprzyja tworzeniu atmosfery opartej na wzajemnym zaufaniu, co z kolei przekłada się na bardziej efektywną i harmonijną współpracę. Budowanie pozytywnych relacji, opartych na otwartej komunikacji i wzajemnym szacunku, umacnia poczucie przynależności do zespołu. Co więcej, pracownicy, czując się docenieni i wysłuchani, z większym entuzjazmem angażują się w realizację strategicznych celów firmy, co w naturalny sposób przekłada się na lepszą atmosferę w całej organizacji.
W jaki sposób Lean zajmuje się ludźmi w organizacji?
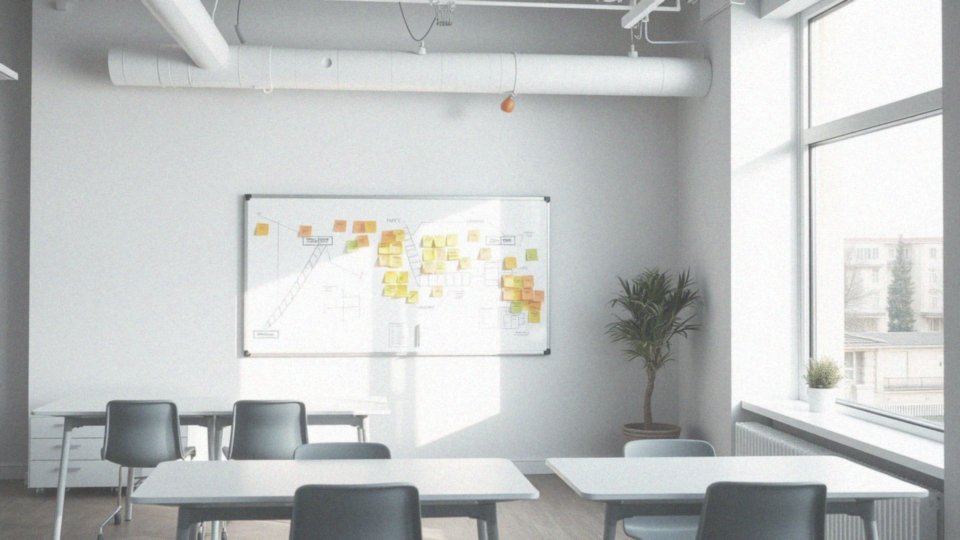
Lean postrzega swoich pracowników jako kluczowy element, który napędza sukces firmy, dając im autentyczny wpływ na jej kierunek rozwoju. Filozofia ta wyposaża ich w niezbędne narzędzia, pogłębia ich wiedzę i obdarza odpowiednimi uprawnieniami, co pozwala im skutecznie:
- identyfikować przeszkody,
- znajdować przemyślane rozwiązania.
Co więcej, sprzyja oddolnym inicjatywom, zachęcając pracowników do dzielenia się swoimi pomysłami i sugestiami usprawnień. W ten sposób budowane jest środowisko pracy, w którym panuje zaufanie i efektywna współpraca. Lean stwarza warunki do nieustannego rozwoju kompetencji, angażując pracowników w proces podejmowania decyzji, co w konsekwencji wzmacnia ich identyfikację z firmą. Liderzy Lean Management kształtują atmosferę, w której sami pracownicy z własnej inicjatywy zgłaszają problemy, co z kolei podnosi ich zaangażowanie i poczucie odpowiedzialności. Aktywne rozwiązywanie wyzwań daje pracownikom realny wpływ na trajektorię rozwoju przedsiębiorstwa, tworząc w ten sposób kulturę ciągłego doskonalenia. Przykładowo, pracownik może zaproponować innowacyjne rozwiązanie optymalizacyjne dla konkretnego procesu, a następnie aktywnie uczestniczyć w jego wdrażaniu.
Jak monitorować postępy w transformacji Lean?
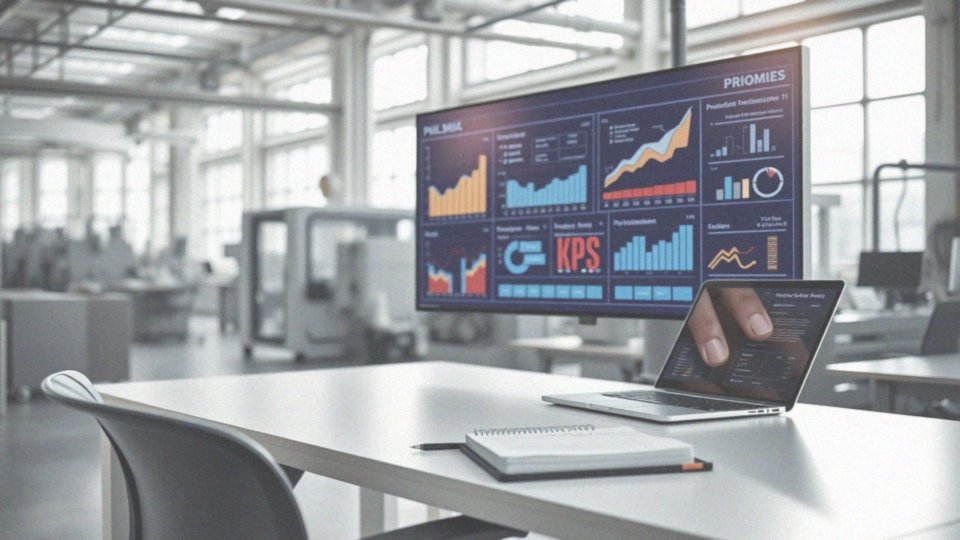
Aby z sukcesem monitorować postępy we wdrażaniu Lean, niezbędne jest określenie odpowiednich Kluczowych Wskaźników Efektywności (KPI). Te wskaźniki pozwalają na obiektywną ocenę skuteczności wprowadzanych zmian i identyfikację obszarów wymagających dalszych udoskonaleń. Kluczowe znaczenie ma tutaj ciągłe gromadzenie i analizowanie danych. Oprócz śledzenia wskaźników, równie ważne są:
- regularne kontrole,
- ocena zaangażowania pracowników,
- monitorowanie osiąganych oszczędności.
Wybierając KPI, należy pamiętać, aby były one ściśle powiązane z celami Lean, takimi jak optymalizacja procesów, minimalizacja marnotrawstwa czy podnoszenie jakości. Wybrane wskaźniki powinny być mierzalne, wiarygodne i zrozumiałe dla wszystkich. Przykładowo, w monitoringu Lean często wykorzystuje się KPI takie jak:
- skrócenie czasu cyklu produkcyjnego,
- zmniejszenie ilości wadliwych produktów,
- wzrost wydajności,
- szybsze przezbrojenia,
- poprawa rotacji zapasów.
Systematyczna analiza zebranych danych pozwala na precyzyjne wskazanie obszarów, które wymagają optymalizacji. Istotne jest, by decyzje dotyczące działań naprawczych opierały się na solidnych i aktualnych informacjach. Podsumowując, rzetelne monitorowanie KPI stanowi fundament sukcesu transformacji Lean.